SCADA Systems: The Backbone of Modern Industrial Automation
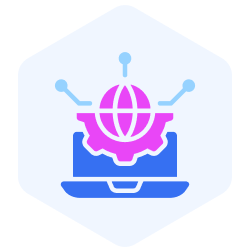
SCADA Systems: The Backbone of Modern Industrial Automation
SCADA, or Supervisory Control and Data Acquisition, is a system that monitors and manages industrial processes. It collects data from sensors and machines, processes the information, and displays it in a way that operators can easily understand. These systems are widely used in industries like manufacturing, energy, and water management to monitor operations and ensure smooth operation. SCADA helps operators see what’s happening in real time and take action if something goes wrong.
History and Evolution of SCADA Systems
SCADA systems emerged in the 1950s when industries started using basic tools to monitor equipment remotely. At the time, these systems were simple and relied on wired connections to send and receive data. As computers became more common in the 1970s, SCADA systems advanced, including centralized control rooms and graphical displays.
By the 1990s, SCADA had taken another leap with networked systems that could handle larger-scale operations. In recent years, technologies like cloud computing and IoT have given SCADA a modern edge in handling big data and connecting to smart devices.
How does SCADA work?
SCADA systems are like the control center for industrial processes. They collect data from machines and sensors, send it to a central system, and display it in a way that operators can easily understand. If something goes wrong, operators can quickly take action. The system also sends commands back to the machines to adjust how they work when needed. The whole system consists of the following core components:
Supervisory System: This is the brain of SCADA, where all the data is processed and displayed. Operators use it to monitor and control everything from one place.
Remote Terminal Units (RTUs): These devices are spread out in the field to collect data and send it to the central system. They act like messengers between machines and the supervisory system.
Programmable Logic Controllers (PLCs) are specialized computers that automate specific tasks, such as opening or closing a valve. They work alongside RTUs to control equipment.
Communication Infrastructure: This is the network that connects everything. Depending on the setup, it could consist of cables, radio signals, or satellite links.
Human-machine interface (HMI): The HMI is the dashboard operators use to monitor their operations. It displays data in an easy-to-read format, such as graphs, alarms, or real-time visualizations.
Figure- SCADA Architecture Diagram.png
Figure: SCADA Architecture Diagram
The SCADA system operates through a series of interconnected steps, from data collection in the field to centralized monitoring and control:
Sensors and controllers, like Remote Terminal Units (RTUs) and Programmable Logic Controllers (PLCs), gather data from equipment, such as temperature, pressure, or speed.
This data is sent to a Supervisory System using the Communication Infrastructure, which could include wired or wireless networks.
The supervisory system processes and displays the data on the Human-Machine Interface (HMI). This is where operators see graphs, charts, or alerts showing what’s happening in real-time.
If adjustments are needed, operators can send commands back through the system, creating a feedback loop. For example, if a pump runs too fast, SCADA can slow it down.
Benefits of SCADA Systems
Here are the key advantages of SCADA in industries, along with specific examples:
1. Real-Time Monitoring and Control
SCADA systems provide a live view of operations, allowing operators to monitor processes and take immediate action when necessary. For example, in a power grid, SCADA can track voltage levels and instantly alert operators if there’s an abnormal fluctuation. Operators can then remotely adjust settings to avoid outages or equipment damage and ensure an uninterrupted power supply.
2. Improved Operational Efficiency and Productivity
SCADA helps industries save time and resources by automating repetitive tasks and providing a centralized control system. In a manufacturing plant, for instance, SCADA can automate the process of filling bottles on a production line, reducing the need for manual supervision. The workforce can then focus on more complex tasks, ultimately boosting productivity.
3. Enhanced Decision-Making with Data Analytics
SCADA systems gather and store vast amounts of data over time, which can be analyzed to optimize operations. For example, in water treatment facilities, historical data on water usage patterns can help predict demand and adjust operations to prevent wastage. This data-driven approach supports smarter decisions, like scheduling maintenance during low-demand periods.
4. Reduced Downtime and Maintenance Costs
SCADA systems help identify potential issues before they lead to major failures. In oil pipelines, SCADA can detect small leaks by monitoring pressure changes in real-time. Early detection means repairs can be scheduled immediately, reducing downtime and avoiding the high costs associated with major disruptions or environmental damage.
5. Integration with IoT and Modern Technologies
Modern SCADA systems integrate seamlessly with IoT devices and advanced technologies like cloud computing and AI. For instance, in agriculture, IoT-enabled sensors can monitor soil moisture levels and send data to the SCADA system. Farmers can then use this information to optimize irrigation schedules and conserve water while improving crop yields.
Challenges and Limitations
While SCADA systems are incredibly useful, they come with some challenges and limitations that industries need to consider:
1. Security Vulnerabilities
SCADA systems are often connected to networks, which makes them targets for cyberattacks. Hackers could gain access to critical operations, such as power grids or water supply systems, and cause major disruptions. For example, in recent years, there have been cases of ransomware attacks targeting industrial systems, forcing companies to temporarily shut down operations. Keeping SCADA systems secure requires constant updates and strong cybersecurity measures.
2. High Setup and Maintenance Costs
Setting up a SCADA system can be expensive. The cost of hardware like sensors, controllers, and servers, combined with software and installation, adds up quickly. In addition, maintaining the system over time—replacing old equipment, upgrading software, and training staff—requires ongoing investment. This can be a big hurdle for smaller companies with limited budgets.
3. Complex System Integration
SCADA systems often need to work alongside other technologies and older equipment, which can make integration complicated. For example, if a factory has machines from different manufacturers, getting them all to communicate smoothly within the SCADA system can take time and expertise. If the integration isn’t done properly, it could lead to errors or delays.
4. Dependence on Reliable Communication Networks
SCADA relies on communication networks to transmit data between field devices and the central control system. If the network goes down—due to bad weather, hardware failure, or even simple outages—the entire system’s functionality is affected. For instance, in a remote oil field, a loss of communication could mean operators can’t monitor pipelines or respond to issues until the network is restored.
Real-World Use Cases of SCADA
SCADA systems play a vital role in many industries, helping to monitor and control complex operations. Here are some real-world examples of how SCADA is used:
1. Energy Management
SCADA is widely used in power grids to monitor electricity flow and detect outages. For example, utility companies use SCADA to track voltage levels and automatically reroute power in case of a fault, reducing downtime for customers. It’s also used in renewable energy systems, like solar farms and wind turbines, to monitor performance and ensure energy is being fed into the grid efficiently.
2. Water and Wastewater Treatment
SCADA systems monitor water levels, pressure, and chemical usage in water treatment plants. For instance, SCADA can automatically adjust the chlorine levels in a water supply to maintain safe drinking standards. It’s also used to track pump performance in wastewater facilities.
3. Manufacturing and Production Automation
SCADA helps factories keep their production lines running smoothly. For example, in an automobile plant, SCADA can monitor robotic arms on the assembly line and ensure they work in sync. If a machine overheats or malfunctions, the system can alert operators immediately Hence, it minimizes production delays.
4. Oil and Gas Monitoring and Control
In the oil and gas industry, SCADA oversees pipelines, storage tanks, and refining processes. For example, SCADA can detect a drop in pressure within a pipeline and signal a potential leak. Operators can then shut down the affected section and repair it before it becomes a major problem. SCADA is also used to track inventory levels in storage tanks and automate refilling processes.
5. Transportation and Logistics
In transportation systems, such as rail networks and airports, SCADA systems monitor train signals, track power usage in electrified rail systems, and ensure safety measures are working properly. In logistics, SCADA can monitor conveyor belts in warehouses to keep the goods moving efficiently and prevent bottlenecks.
Future of SCADA
SCADA systems are evolving rapidly due to advancements in technology. Here’s a look at the trends and innovations that are shaping the future of SCADA:
1. Integration with IoT, Cloud, and Edge
Modern SCADA systems go beyond basic monitoring and control. Technologies like the Internet of Things (IoT), edge computing, fog computing, and cloud platforms are making SCADA systems smarter and more connected. IoT sensors collect data from remote locations, while cloud integration allows access to this data from anywhere.
2. Potential Impact of AI, Blockchain, and 5G
Artificial intelligence (AI) algorithms can analyze large amounts of data collected by SCADA systems to predict failures before they occur or optimize processes for greater efficiency. For instance, AI could identify patterns in machinery behavior that indicate a breakdown.
Blockchain technology adds another layer of security by ensuring data integrity. For industries like energy and transportation, blockchain can help track data across SCADA systems without the risk of tampering.
5G networks facilitate faster and more reliable communication. With 5G, data from sensors and devices can be transmitted almost instantly, making real-time monitoring even more accurate. This is useful for large-scale operations like smart grids or oil pipelines that require quick responses.
3. Predictions for SCADA in Industry 5.0
As Industry 5.0 evolves, SCADA systems are expected to become more human-centric. This means combining the precision of automation with human creativity and decision-making. In the future, SCADA systems could work alongside collaborative robots (cobots) in manufacturing or provide operators with augmented reality (AR) interfaces to visualize operations in real-time.
There’s also a focus on sustainability. SCADA systems will likely play a major role in managing renewable energy resources, reducing waste, and supporting green initiatives across industries.
Conclusion
SCADA systems are the backbone of modern industrial automation that enables real-time monitoring, control, and data-driven decision-making across various sectors. From managing energy grids and water systems to optimizing production lines and monitoring pipelines, SCADA plays a critical role in ensuring smooth and efficient operations. While it has challenges like cybersecurity risks and high setup costs, ongoing advancements in technologies like AI, IoT, and 5G are shaping its future, making it smarter and more connected. As industries continue to evolve toward Industry 5.0, SCADA will remain a foundation that bridges human oversight with advanced automation to create more sustainable and innovative solutions.
FAQs on SCADA
1. What is SCADA, and why is it important?
SCADA is a system that monitors and controls industrial processes in real time. It helps industries manage complex operations like power grids, water treatment plants, and manufacturing lines for smooth operations and reliable performance.
2. How does SCADA work in industrial processes?
SCADA collects data from sensors and controllers, transmits it through networks, and displays it on a central interface for operators. Operators can monitor processes, analyze data, and send commands back to machinery to adjust operations when needed.
3. What industries rely on SCADA systems?
SCADA is used in many industries, including energy (to manage power grids and renewable energy), water and wastewater treatment, manufacturing, oil and gas monitoring, and transportation systems like rail networks and traffic control.
4. What are the challenges of using SCADA systems?
Some challenges include security vulnerabilities, such as susceptibility to cyberattacks, high costs for setup and maintenance, complexity in integrating with other systems, and dependence on reliable communication networks.
5. How is SCADA evolving with modern technologies?
SCADA integrates with technologies like AI, IoT, blockchain, and 5G. AI helps with predictive maintenance and process optimization, IoT improves data collection from remote locations, blockchain enhances data security, and 5G enables faster communication for real-time operations.
Related Resources
- History and Evolution of SCADA Systems
- How does SCADA work?
- Benefits of SCADA Systems
- Challenges and Limitations
- Real-World Use Cases of SCADA
- Future of SCADA
- Conclusion
- FAQs on SCADA
- Related Resources
Content
Start Free, Scale Easily
Try the fully-managed vector database built for your GenAI applications.
Try Zilliz Cloud for Free